
What Is the Power Behind a Diaphragm Hydrogen Compressor?
A diaphragm hydrogen compressor is a powerful machine that uses pressure to increase the density of hydrogen gas. It's used in many industrial applications, such as in power plants and refineries, and offers some unique benefits. But what is the real power behind this type of compressor? The main force driving a diaphragm hydrogen compressor is its high pressure capability. The higher the pressure it can generate, the more efficiently it can compress hydrogen gas. This means that more energy can be extracted from each sector of air than with other types of compression systems. Additionally, they are able to reach pressures up to 10 times greater than standard piston or rotary compressors! Moreover, these compressors are also designed to minimize maintenance costs and ensure long-term reliability. The design eliminates wear on components since most of the work is done by increasing or decreasing hydraulic pressure rather than mechanical friction between moving parts. This makes them ideal for places where downtime must be kept to a minimum. Furthermore, diaphragm hydrogen compressors are also incredibly quiet when compared to other types of machines. This makes them suitable for use in residential
read more
How to Unlock Unbeatable Power with a Diaphragm Hydrogen Compressor
Have you ever wanted to unlock unbeatable power with a diaphragm hydrogen compressor? Well, it's possible! There are several key steps that must be taken in order to do this. Firstly, you need to form an airtight seal around the diaphragm. This can be done using a rubber gasket or grease. Next, attach the compressor onto the cylinder head and ensure all of the connecting bolts are tight (it is essential to avoid leaks). The third step is to connect the fuel line from the tank into the intake manifold of the engine. This will allow for fuel delivery into the combustion chamber. Lastly, start up your engine and let it warm up until it runs smoothly before engaging full throttle! Now that we have taken care of pre-compression requirements, let's move on to compression itself. You should adjust your air/fuel ratio according to manufacturer specifications or risk damaging your engine components. Then set your desired boost level by adjusting pressure within your system (this can be done with a pressure gauge) and begin compressing air molecules into tiny particles with tremendous force. Keep an eye out for any abnormal noises coming from your engine while doing
read more
Benefits of Using Diaphragm Hydrogen Compressors
The use of diaphragm hydrogen compressors can be incredibly beneficial for any number of applications. These devices are small in size, yet effective and efficient in their performance, making them ideal for a wide range of needs. Not only do they help reduce noise levels, but they also provide increased safety when used properly. In addition, these compressors can even help to save energy costs over time! One major benefit of using diaphragm hydrogen compressors is the low operating cost associated with them. Most models have minimal maintenance requirements and run on relatively cheap fuel sources such as natural gas or propane. This helps lower overall operational expenses and makes them more affordable for everyday use. Additionally, they are designed to last for years without needing replacement parts or added services. Another advantage that comes with diaphragm hydrogen compressors is the improved safety they provide when compared to other types of air compressors like reciprocating ones. Since the operation requires less pressure and electricity than other machines, there is a much lower chance of accidental explosions or fires due to overheating systems. Plus, these devices don't produce as much heat during operation, so
read more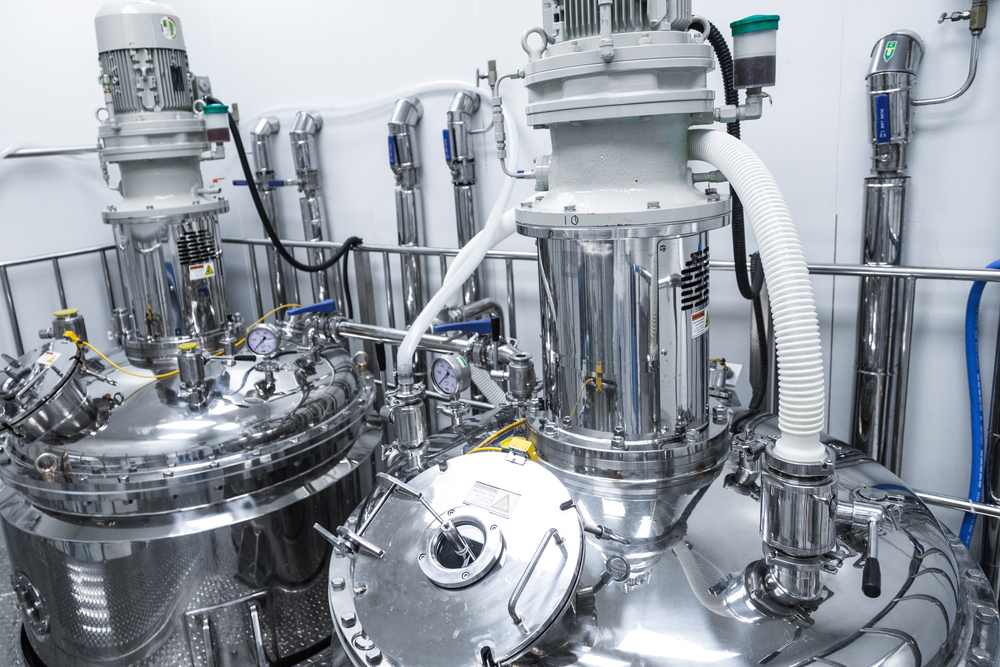
Design and Operation of Diaphragm Hydrogen Compressors
Design and Operation of Diaphragm Hydrogen Compressors is a complex process. It requires careful consideration when designing and operating them for optimal performance! This involves selecting the right materials, balancing between safety and efficiency, as well as managing pressure levels. (The first step in this process is to choose the type of diaphragm material that best suits the application.) The most common materials used are polymers such as neoprene or nitrile rubber. These materials offer excellent resistance to abrasion and corrosion, making them a great choice for hydrogen compressors. Moreover, the design must also take into account the environment it will be exposed to. High-temperature applications may require special insulation or cooling systems while low-temperature environments may necessitate additional safeguards against frost damage. (It's important to make sure that all components are designed to withstand these extreme conditions.) Additionally, careful selection of seals and gaskets can help prevent gas leakage while still providing a reliable seal. Furthermore, proper balance between safety and efficiency must be maintained during operation of diaphragm hydrogen compressors. This entails regularly checking pressure levels and adjusting accordingly if needed. (For example, if the pressure level drops below the acceptable
read more